EXPERT INSIGHT
Fast Innovation in Medtech: The Role of Additive Manufacturing

Innovation in medical technology is a race to help patients with better instruments, devices, and machinery. But to do so safely and at a cost healthcare systems and patients can afford. Additive manufacturing (AM) can play a key role at the intersection of these often conflicting demands. Here’s how and why medtech innovators use certified AM, in particular, to get better devices to market faster.
The potential for AM across medical applications is well understood. The opportunity to deliver highly personalized care where this has not been possible before is embraced by clinicians and surgeons around the world — from revolutionizing complex operations to tailoring implants and prostheses.
What’s less well known is the degree to which AM can support the development and manufacture of standard devices from prototype to series production.
Outsourced additive manufacturing, certified to comply with a range of regulations, opens up new opportunities for medtech businesses to innovate — and find the best and fastest way to make new-and-improved, patient-safe products.
A series of one, or unlimited series of one
AM means no expensive tooling, which means no minimum order quantity, no small series penalty.
Simply put, a functional, true-to-life prototype, safe for clinical testing, can be made quickly using a wide range of approved materials.
The advantage is clear: instead of making one very expensive prototype very slowly, AM can quickly give product development teams multiple prototypes to test design variations and run through fast iterations. GOGOA's HANK exoskeleton is a shining example of small series manufacturing, creating personalized devices to help patients with gait rehabilitation with 15 3D-printed parts (seen in the header image).
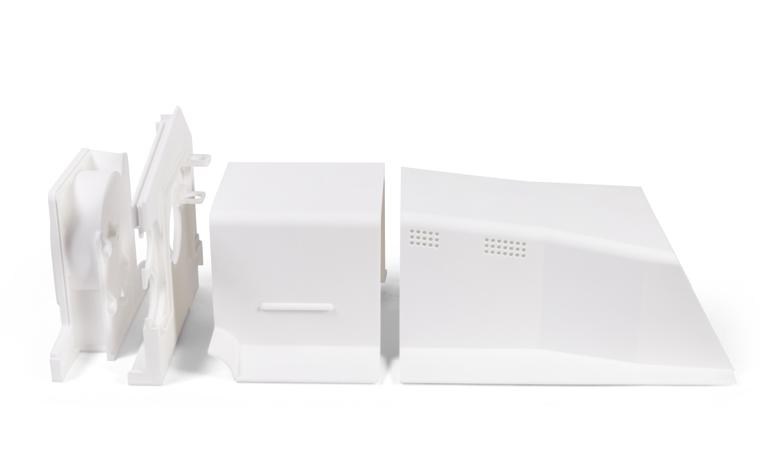
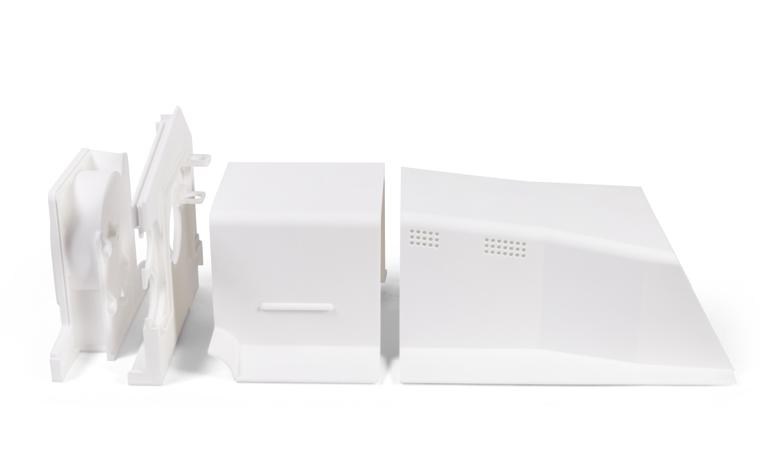
No waiting around for tools: a bridge into full series
Many medtech businesses use certified outsourced AM to bring forward series production, even for parts and instruments that will later be made using conventional manufacturing methods, such as die casting or injection molding.
Tooling, sourcing, and setting up production for a new device can take up significant time. Time lost in getting the product to market. Certified AM can bridge this gap, ensuring that you can manufacture an initial series as soon as the design is final and while tools are being made.
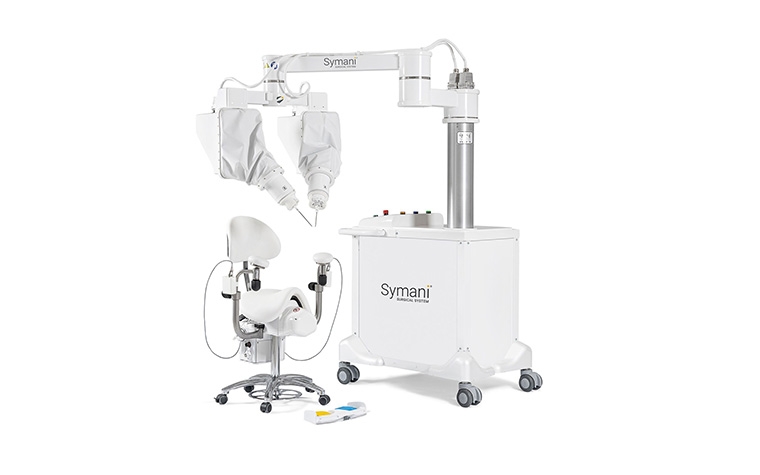
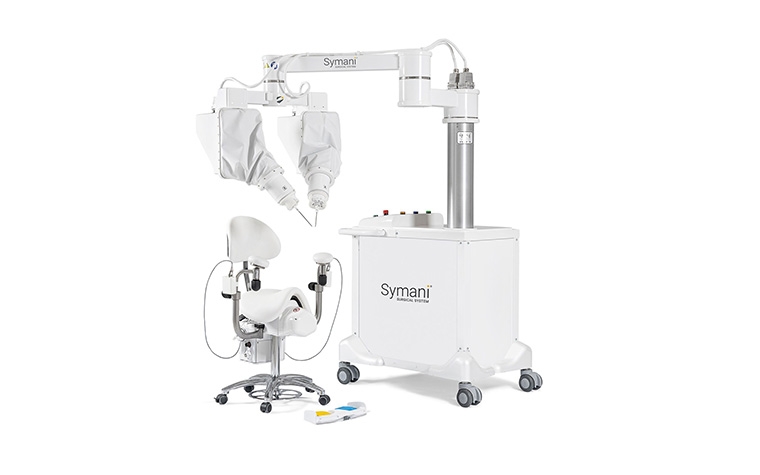
Equally, where occasional smaller runs of a product are always the requirement, these can be made on demand using AM rather than at the high minimum volume demanded by manufacturing processes with tooling.
On-demand small series production can also shift the economic equation in favor of reshoring manufacturing closer to where the devices are needed and away from “economical at high-volume” locations, whether that’s to reduce transport, to support ESG goals, or to cushion or eliminate supply chain risk.
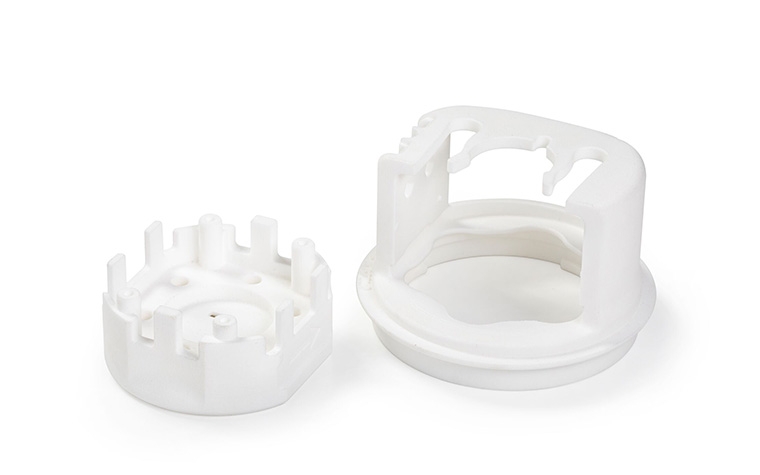
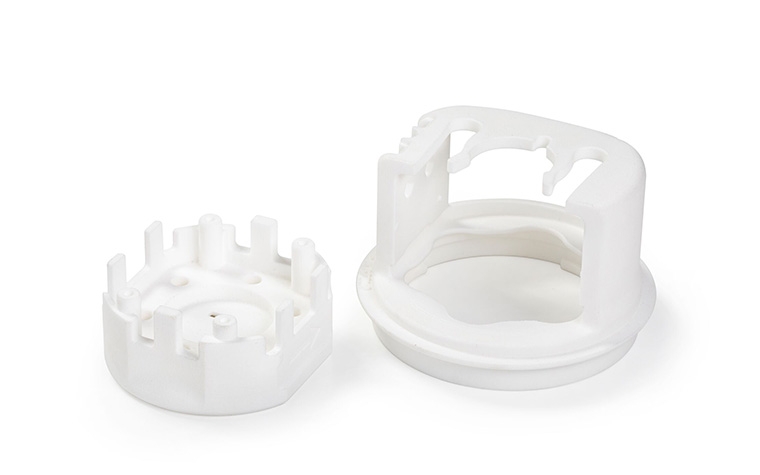
Innovating in partnership
Certified AM partners can support R&D teams with design for AM, technology and compliance knowledge, and optimizing, integrating, and testing. They can also help identify the right materials, textures, and methods.
AM partners often cover a broad range of additive technologies, which means development teams are not locked into or have to make decisions about a specific material or technology too early in the process.
Where AM partners understand the compliance demands of medical device manufacture in all its degrees and nuances, they can help interpret and advise regulations to ensure the best, most economical manufacturing process is chosen for a given product, with proportionate quality management and process control.
Certified AM gives medtech innovators extra speed and flexibility during product development and into series production, without small-volume cost penalties.
The ability to quickly test prototype options enables a faster evolution of device design and, ultimately, a better product for the patient.
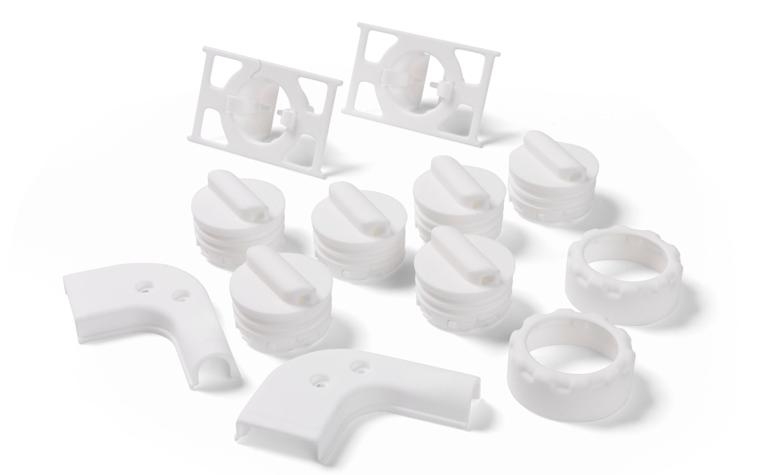
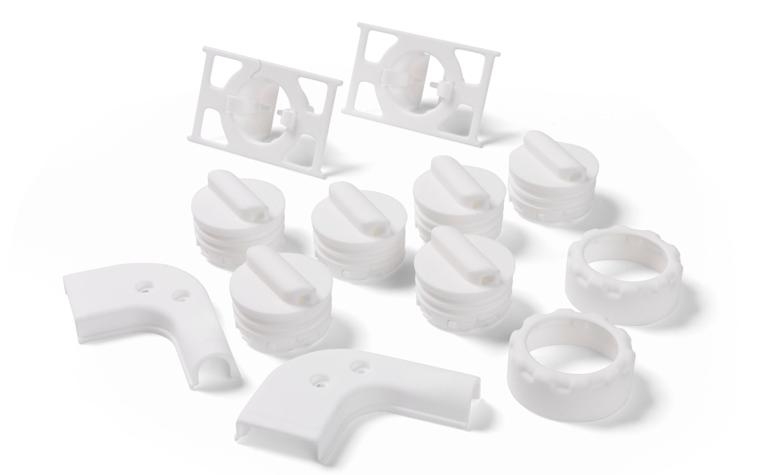
Header image credit: Gogoa Mobility Robots
Share on:
You might also like
Never miss a story like this. Get curated content delivered straight to your inbox.