Webinar
From Identifying AM Parts to Streamlining Production
How to optimize AM processes and accelerate time-to-market
About this webinar
Qualifying additive manufacturing (AM) parts can be a lengthy and time-consuming process. Evaluating profitability and selecting the most suitable materials requires expertise and extensive analysis, involving both design and financial considerations. Once parts have been identified for 3D printing, collaboration between internal customers, supply chain teams, and AM champions can become complex. Without a proper AM operating system, streamlining the definition of requirements and getting visibility of the concept-to-production cycle may lead to delays and miscommunication.
In this webinar, you will learn how to optimize AM processes by automatically selecting the right parts for 3D printing using the integrated CASTOR software within the Materialise CO-AM Software Platform.
What you will learn
- How you can automatically choose the optimal parts for 3D printing from thousands of options, considering material properties, cost-effectiveness, and digital supply chain benefits
- How to accelerate production timelines and reduce time-to-market for your additive manufacturing projects
- How to enhance collaboration and communication through seamless data transfer and real-time tracking with the Materialise CO-AM Software Platform
- How to explore the benefits of a digitally connected experience from part identification to order entry and part delivery
Speakers
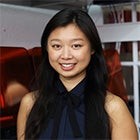
Janet Kar

Ido Green

Kyle Adriany
Share on: