Eyewear Manufacturing
Power of a factory, quality of an atelier
As an industry and as a product, eyewear has unique requirements that need to be mastered to deliver reliable, repeatable, and scalable quality. Our dedicated production line for 3D-printed eyewear, developed specifically to meet these exacting demands and evolving continuously, means we have the trusted infrastructure and teams to support you at whatever stage you’re at.

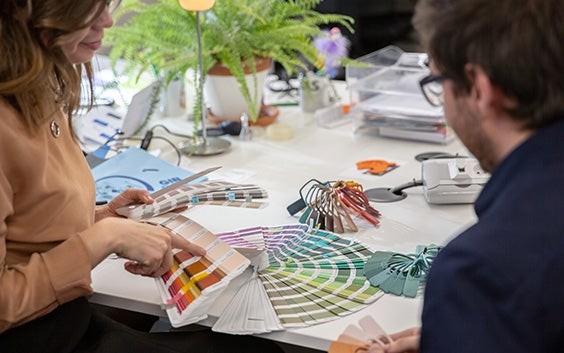
Meet your team
To successfully bring a new concept to life, you need to surround yourself with people who know exactly what they’re doing. When you partner with Materialise, you get a dedicated production team who are specialized in every aspect of creating eyewear. Drawing on their vast experience supporting some of the industry’s most progressive eyewear brands, they can guide you throughout the journey.
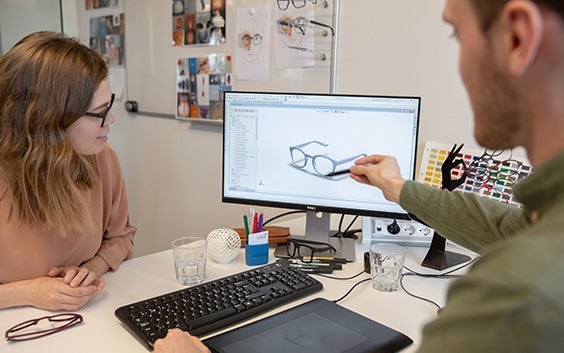
An NPI process you can rely on
Our detailed new product introduction (NPI) process takes you step-by-step from idea to final product. Together, we’ll assess your requirements, looking at design feasibility and selecting the most suitable materials, colors, and finishes from our vast portfolio. Through prototyping phases, we’ll fine-tune every last detail, so you’re ready for production. And for collections where the designs are already 3D-print ready, our express track can help you go to market in less than two months.
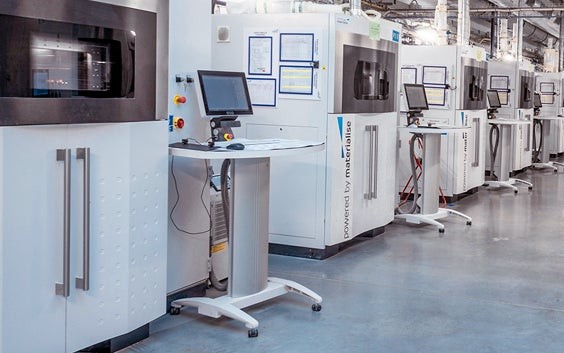
Manufacturing at your scale
Every collection is unique, but every frame demands the same high quality and attention to detail. Over the years, as we have partnered with dozens of businesses, from designer ateliers to mainstream consumer brands, we have honed our 3D printing process to the exacting requirements of the eyewear industry.
Our series of designated machines are tuned specifically for 3D printing eyewear frames. And with our in-house software expertise, we use advanced parameter control to maintain tight tolerances and deliver superior quality, so every frame off the machine is the same, every time we print it.
What’s more, we fine-tune the process to the smallest detail in line with your specific collection requirements.
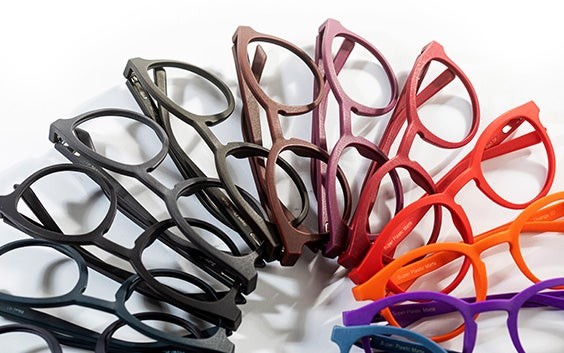
Perfecting your frames
Once your frames are ‘off the machine,’ they go through extensive post-processing steps to turn them into the finished pieces that will delight your customers. Your selection of colors and surface finishes are applied with meticulous attention to detail, handcrafted by our in-house team of finishing specialists. And from final assembly to engraving, your frames are finished to perfection.
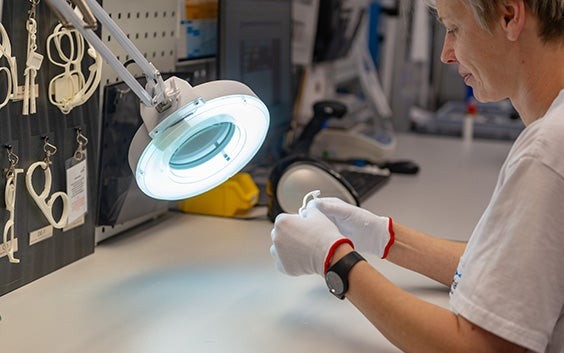
Quality control
Your brand prides itself on delivering quality eyewear, and Materialise is committed to helping you live up to your promises. Certified to ISO 9001 and ISO 14001 standards, amongst others, our pursuit of excellence runs through everything we do, from the tools and technologies we use to the processes we follow and the people who are beside you every step of the way.
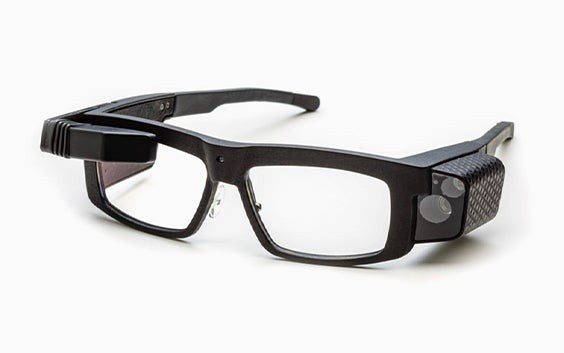
Making eyewear smart
From helping sports enthusiasts with performance monitoring to ensuring field-based operatives can do their jobs safely and effectively, the market for smart eyewear is taking off. 3D printing lets you house complex integrated electronics without compromising on aesthetics or comfort. And with on-demand printing, iterating your designs to keep pace with the tech is perfectly possible.
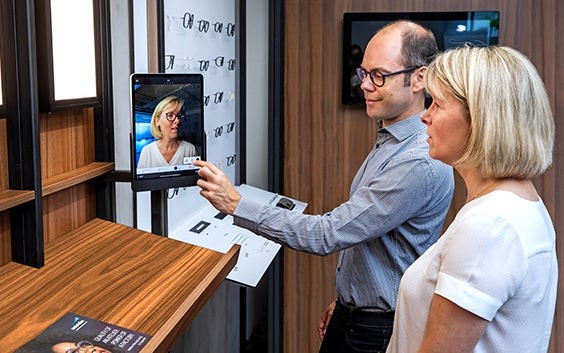
Eyewear Fitting Suite
Choosing a pair of glasses can be a highly intimate experience; the chosen frame becomes an extension of our personality, telling a story without words. Beyond aesthetics, finding the right fit also matters for comfort and visual performance.
By integrating our Eyewear Fitting Suite into your offering, you can deliver a new dimension of personalized service. The in-store platform scans the customer’s face and creates an anatomically exact 3D model.
Together with the optician, the customer can then play with shapes, colors, sizes, or whatever options you choose to offer. The result is a highly individual experience that ensures a unique frame, perfectly suited to your customer’s features.